In today’s fast-paced manufacturing world, optimizing work-in-process (WIP) is crucial for staying competitive. From meeting tight production schedules to managing inventory and minimizing costs, the need for real-time visibility has never been greater. Enter RFID labels for WIP—a smart, scalable solution that empowers factories to operate with precision and agility.
Whether you’re an operations manager striving for end-to-end visibility, a plant manager working to reduce downtime, a CFO focused on cost control, or an IT leader overseeing system integration, RFID labels and tags transform your work-in-process (WIP) tracking and improve overall efficiency.
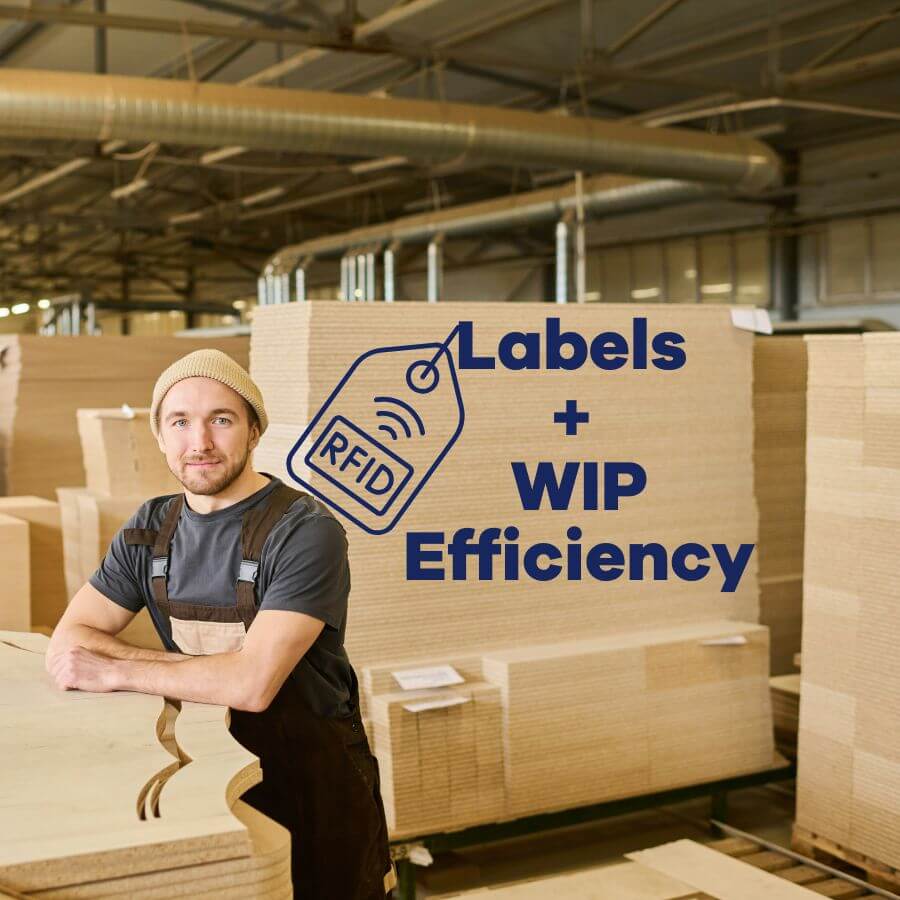
What Is RFID and How Do RFID Labels Work in Manufacturing?
RFID (Radio Frequency Identification) is a wireless technology that tracks assets without requiring line-of-sight. In a factory, RFID labels are affixed to bins, parts, or equipment, and are automatically scanned by RFID readers as items move through production.
Unlike barcodes, RFID can scan multiple items at once—even in high-speed or harsh environments—making it perfect for dynamic production floors.
Solving WIP Challenges with RFID Labels: A Comparison
RFID labels do more than track items—they eliminate guesswork, enable automation, and transform decision-making. Here’s an overview view of common WIP challenges and how RFID labels solve them:
WIP Challenge | RFID Label Solution |
Manual Data Entry Errors |
|
Lack of Real-Time Visibility |
|
Production Bottlenecks |
|
Inventory Discrepancies |
|
Misplaced Components |
|
Limited Process Accountability |
|
Poor Forecasting Accuracy |
|
With RFID for WIP, manufacturers can shift from reactive firefighting to proactive process improvement.
The Cross-Functional Impact of RFID Labels on Manufacturing Efficiency
The benefits of RFID labels for WIP ripple across the entire factory ecosystem. Here’s how key departments capitalize on this technology:
Role | Benefits of RFID for WIP |
Operations Management |
|
Plant Management |
|
Finance & Procurement |
|
IT & Digital Transformation Teams |
|
By aligning technology with operational goals, RFID becomes a cornerstone of smart factory transformation.
Strategic Factors to Consider Before Implementing RFID Labels for WIP
Adopting RFID in a manufacturing environment is more than a tech upgrade—it’s a strategic shift. It requires thoughtful coordination across people, processes, and systems. Common challenges include infrastructure upgrades, validating label performance in different conditions (e.g. wet, metallic, or frozen surfaces), employee training, and integration with existing MES or ERP platforms.
While these hurdles are real, the operational benefits are even greater. For manufacturers seeking agility, traceability, and real-time insight, RFID offers a forward-looking path to operational excellence and Labelink is here to help you make this transition!
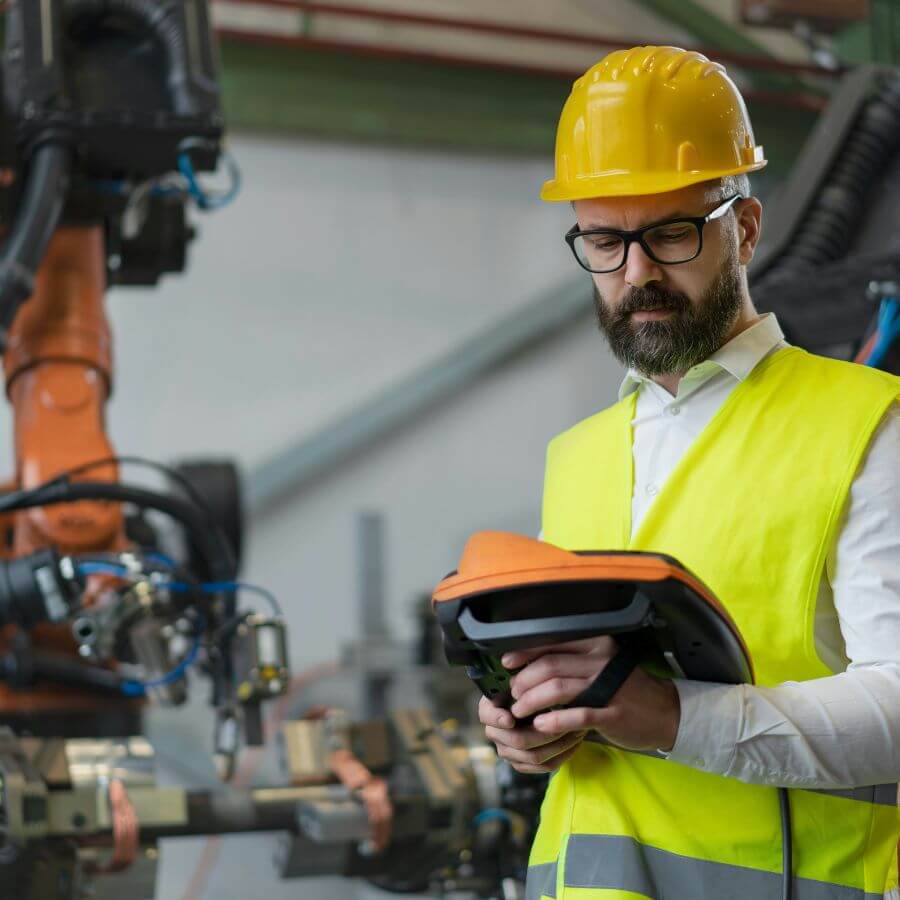
Conclusion: RFID Labels Are Essential for WIP Optimization
Modern manufacturing requires more than just productivity—it demands agility, transparency, and control. By using RFID labels for WIP, factories gain a real-time, unified view of every item on the floor, empowering faster decisions and fewer delays.
For operations leaders, that means smoother workflows. For CFOs, better forecasting and inventory control. For IT teams, a scalable foundation for digital transformation.
If your processes still rely on spreadsheets, barcodes, or independent systems—it’s time to rethink what’s possible. RFID isn’t just a tech upgrade—it’s a strategic leap forward in productivity and profitability. It’s a competitive advantage waiting to be tapped.